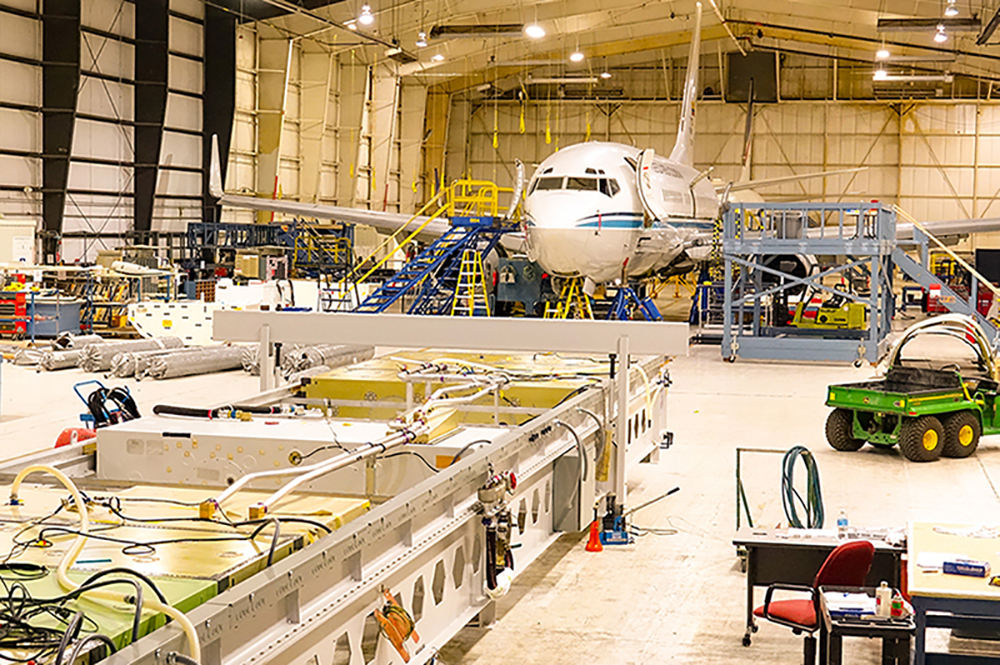
Aircraft repair shops in North America are highly reliant on generic and used parts to keep the jets flying.
The sad state of Airlines and Aircraft repair shops in North America

Both Airlines and Aircraft repair shops in North America are becoming heavily reliant on generic and used parts to keep airplanes flying. The situation is a symptom of climbing costs and supply chain shortages that are plaguing the industry. As per industry analysts and executives, this accounts for a fraction of the estimated $36 billion spent annually on spares, repairs, and sales.
The demand is increasing as aerospace suppliers are struggling to fill new orders while recovering from the pandemic that reduced production and increased labor shortages. Additionally, the higher costs and shortage of new parts are delaying repairs hence pushing airfares. Some brand-name part makes like General Electric Co may benefit from selling used parts or serviceable material. “Companies like GE could lose some demand to such independent companies producing certified components that perform the same fit and function, as they can be cheaper and easier to procure in the current environment,” stated Abdol Moabery. Moabery is the CEO of Florida-based GA Telesis. The firm repairs and overhauls jet engines.
The business of tearing down planes
Several companies are trying to find parts hence driving the demand for “teardown” old planes. “The increase in price for parts is expected to moderate this year after rising between high single-digits and low-double-digits in 2022, even though costs remain above pre-COVID-19 levels,” stated Alex Youngs. Youngs is an executive with Carlyle Group’s repair unit StandardAero, a private equity firm. “The venture has helped the company source parts for older aircraft models that are harder to find in the current market, or are no longer being produced,” revealed a spokesperson.
However, costs are not the only issue. According to Moaberry, the time to turn around some repair orders doubles. This is because it is taking longer to get repaired components. “We used to turn an engine in under 60 days. We’d be lucky to deliver an engine in under 100 days today,” explained Moabery.